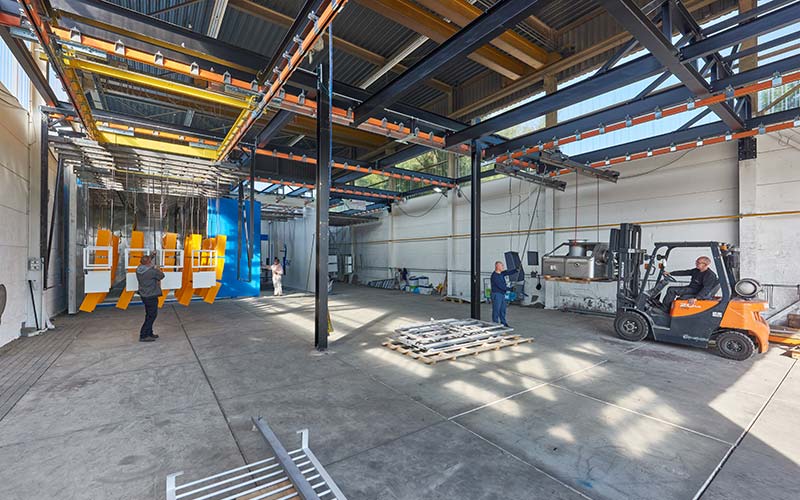
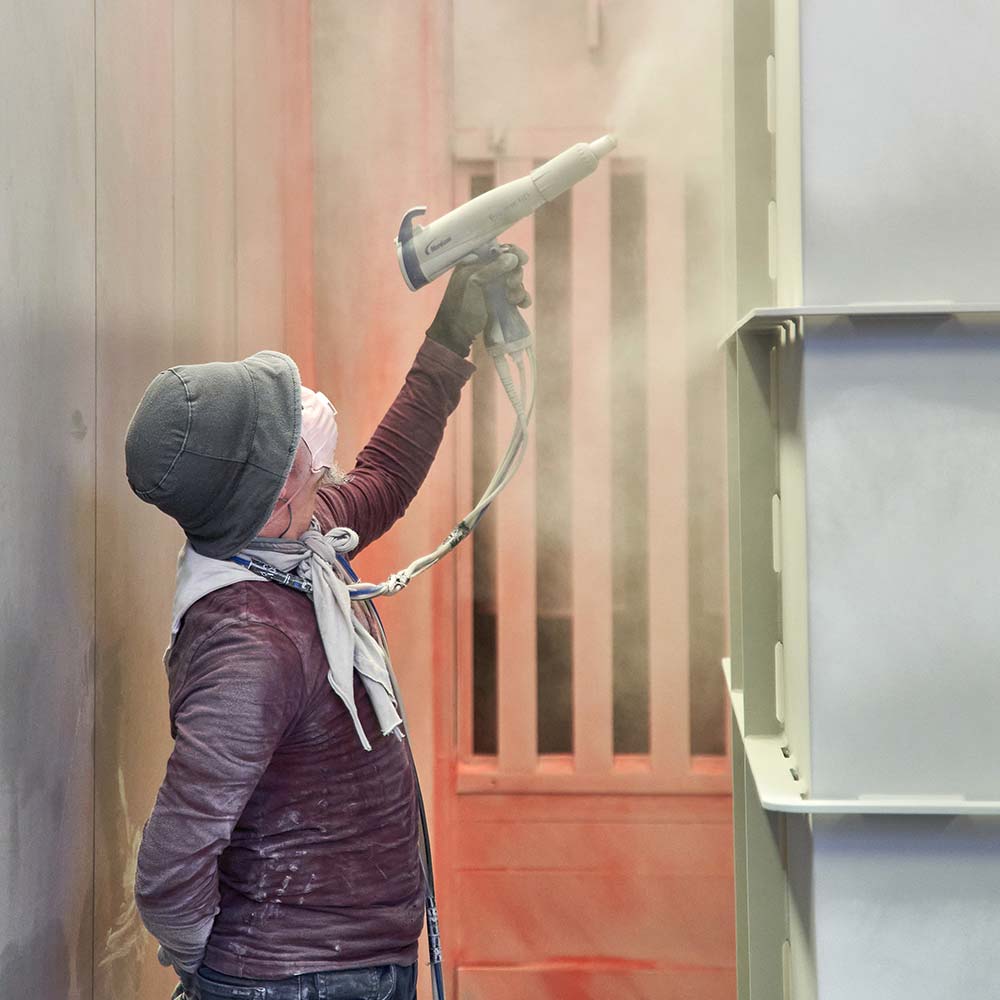
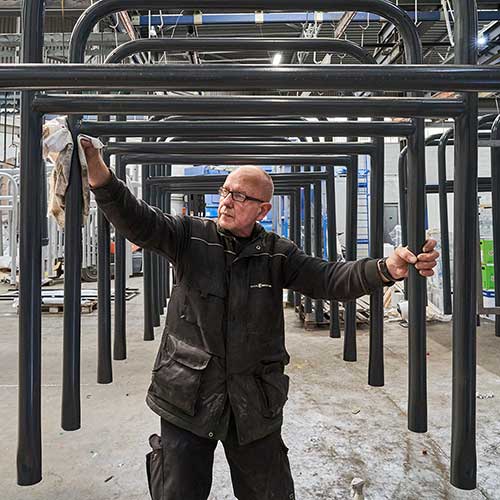
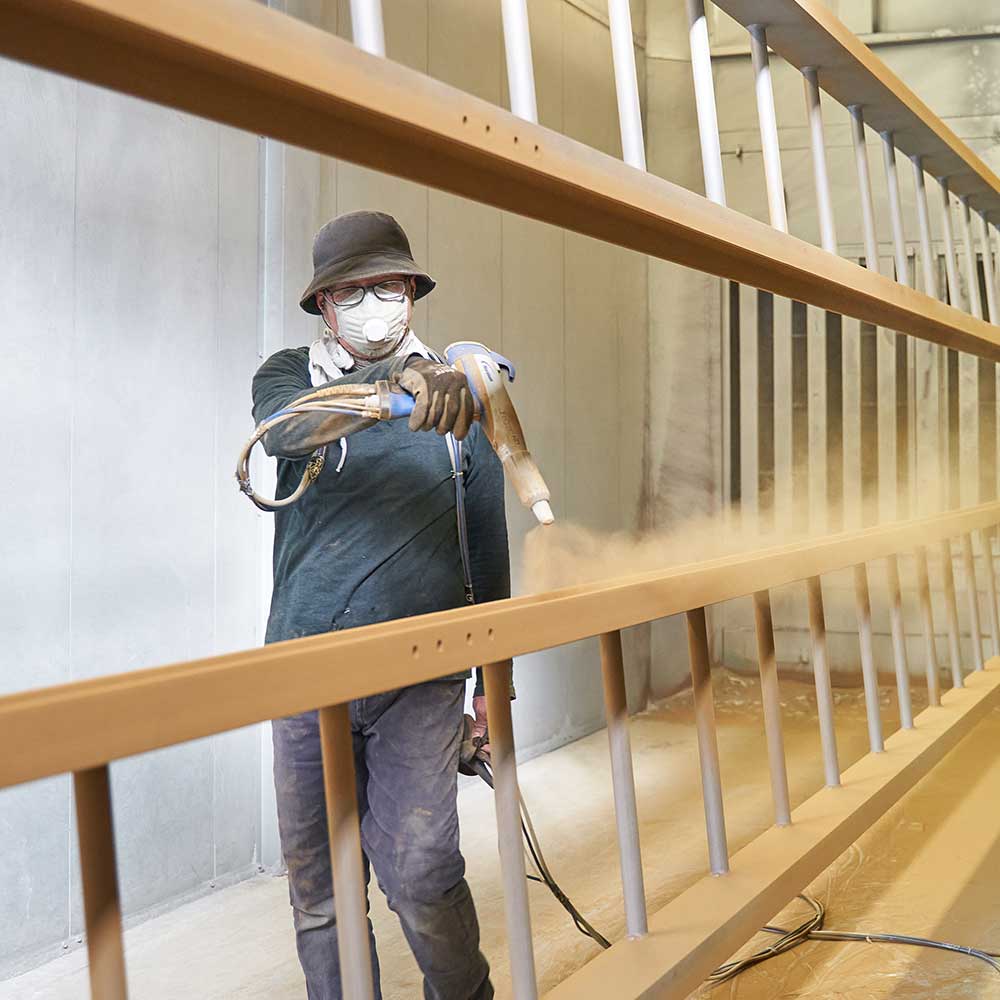
Poedercoaten; stralen met korund voorbehandeling
Poedercoaten is een beschermingsmethode voor metalen voorwerpen. Een goede laag poedercoating beschermt het product tegen externe invloeden die tot bijvoorbeeld corrosie (roestvorming) kunnen leiden. Om zo’n goede laag te krijgen, is de ondergrond heel belangrijk. Daarom beginnen we bij Kalfsvel vrijwel altijd met de voorbehandeling stralen met korund. Dat is een inert straalmiddel (aluminiumoxide) waarmee ook rvs gestraald kan worden. Korund bevat namelijk geen metaaldelen waardoor het geen risico op contactcorrosie geeft.
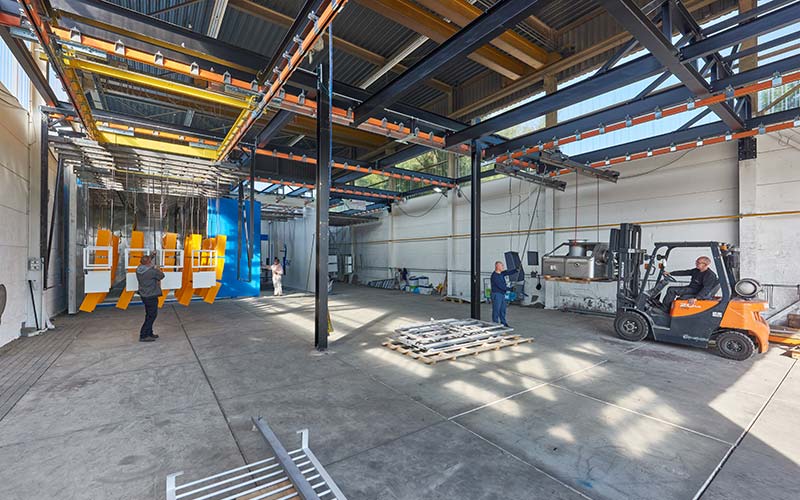
Poedercoaten; stralen met korund voorbehandeling
Poedercoaten is een beschermingsmethode voor metalen voorwerpen. Een goede laag poedercoating beschermt het product tegen externe invloeden die tot bijvoorbeeld corrosie (roestvorming) kunnen leiden. Om zo’n goede laag te krijgen, is de ondergrond heel belangrijk. Daarom beginnen we bij Kalfsvel vrijwel altijd met de voorbehandeling stralen met korund. Dat is een inert straalmiddel (aluminiumoxide) waarmee ook rvs gestraald kan worden. Korund bevat namelijk geen metaaldelen waardoor het geen risico op contactcorrosie geeft.
Maximale hechting voor de hoogste kwaliteit
Door het te gritstralen met korund krijgt het metalen voorwerp een passend ankerprofiel. Het stralen vergroot namelijk het oppervlak doordat er pieken en dalen op aangebracht worden. Dit verzekert de maximale hechting van de poedercoating en zorgt voor een gepoedercoat product van de hoogste kwaliteit. Is het fijnste ankerprofiel gewenst? Dan wordt het product met glasparelen voorbereid.
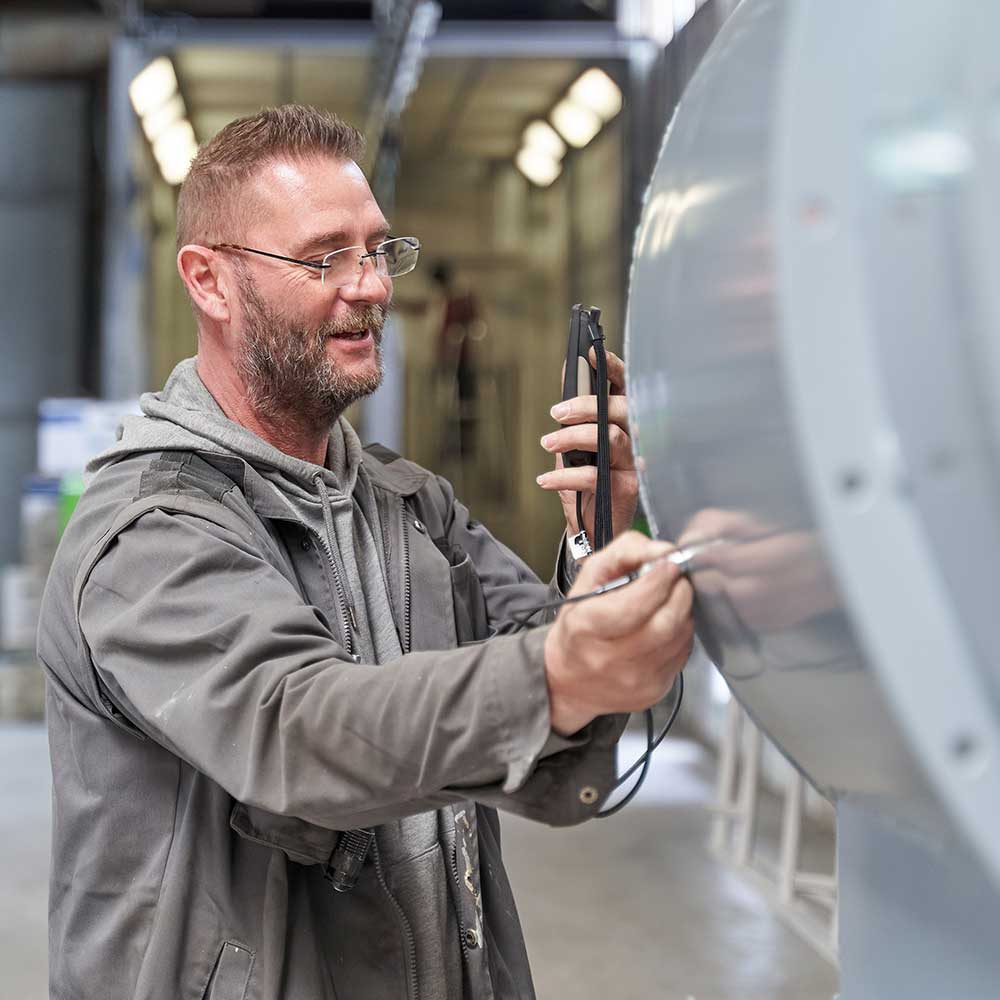
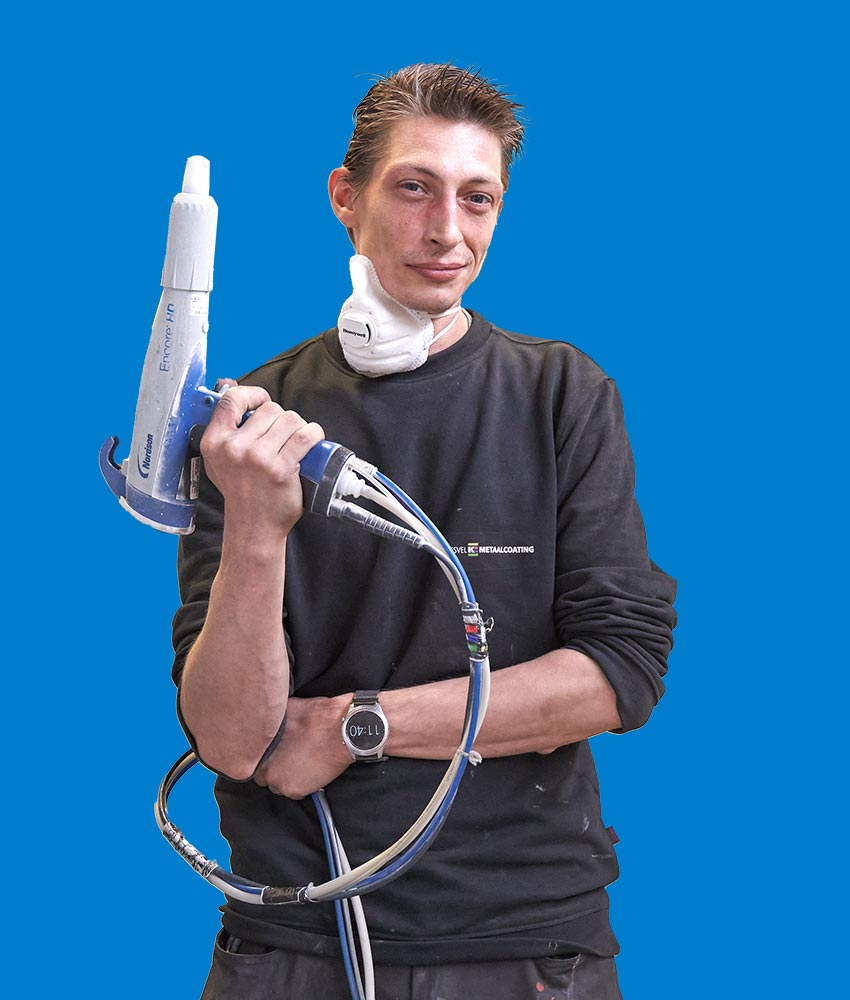
Kalfsvel Metaalcoating; experts in poedercoating
Na de korund-voorbehandeling kunnen we elk metalen object optimaal afwerken met poedercoating. Of het nu meubels zijn of straatmeubilair, industrieel gereedschap of grote, zware staalconstructies. Door de zorgvuldige voorbehandeling en het poedercoaten bij Kalfsvel kan uw product nog jarenlang dienst doen zoals het bedoeld is.
Ontdek de mogelijkheden van poedercoaten bij Kalfsvel
Kalfsvel Metaalcoating; experts in poedercoating
Na de korund-voorbehandeling kunnen we elk metalen object optimaal afwerken met poedercoating. Of het nu meubels zijn of straatmeubilair, industrieel gereedschap of grote, zware staalconstructies. Door de zorgvuldige voorbehandeling en het poedercoaten bij Kalfsvel kan uw product nog jarenlang dienst doen zoals het bedoeld is.
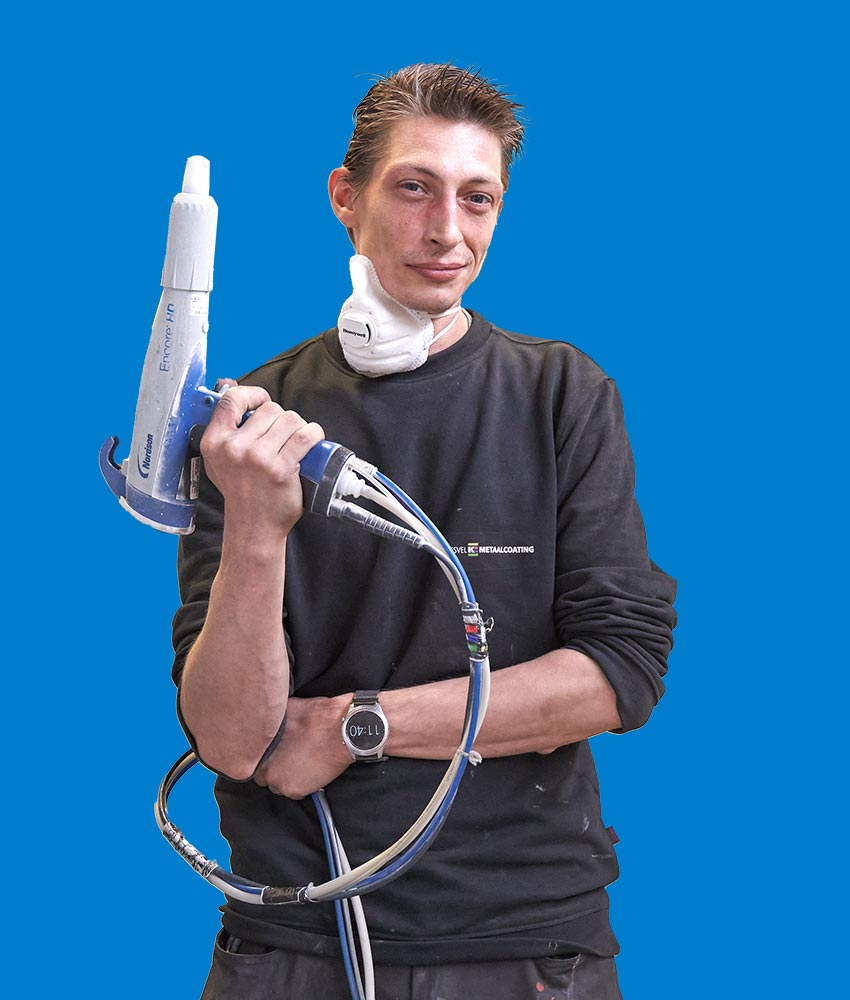
Snel, groot en veel poedercoaten
Met twee poedercoatinstallaties waarvan een tot de grootste in Nederland behoort, hebben we veel capaciteit om te poedercoaten. Onze doorlooptijd is dan ook heel snel; wij kunnen binnen een paar dagen uw product gepoedercoat hebben! Ook als uw product heel groot, heel zwaar of groot en zwaar is. Tot maar liefst 5.000 kg en wel 123 kuub aan materialen en installaties kunnen uw objecten verwerken.
Complexe producten, altijd kwaliteit
De kwaliteit die wij met poedercoating bereiken, blijkt ook uit de complexe producten die we afleveren zoals:
Altijd is een strakke spuittechniek als voorbehandeling vereist om het juiste ankerprofiel met voldoende adhesie te realiseren waarna we het zorgvuldig kunnen afwerken tijdens het poedercoaten zelf. Het is dankzij onze ervaren mensen, de expertise in het proces en de materialen waar wij mee werken dat wij deze kwaliteit in poedercoating steeds weer succesvol kunnen realiseren.
Persoonlijk advies nodig?
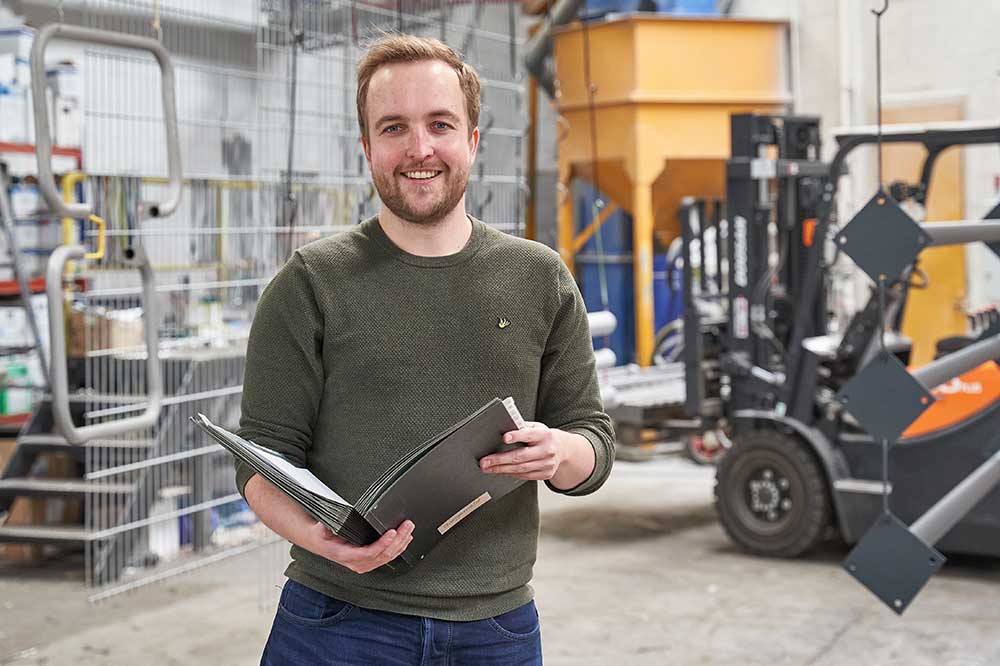
Renovatie met poedercoating
Metalen en verzinkte onderdelen van gebouwen, straatmeubilair en ander langdurig gebruikte objecten, kunnen na een goede renovatie weer opnieuw jaren gebruikt worden. Bij Kalfsvel realiseren we renovatie met poedercoating. Zoals bijvoorbeeld hekwerken van galerijflats in opdracht van VvE’s. Deze materialen worden eerst bij onze partners door middel van een chemische of thermische behandeling van de oude coating ontdaan. Daarna worden ze fijn aangestraald voor het juiste ankerprofiel en voorzien van een speciale epoxy primer. Tenslotte wordt een eindlaag poedercoat aangebracht. Deze manier van duplex coating zorgt ervoor dat het weer voor tientallen jaren behouden is.
Coatingdikte
Poedercoating zelf is een verfpoeder dat onder pulsdruk op een elektrostatisch geaard object wordt gespoten waarna het de oven ingaat. In de oven wordt de poeder vloeibaar en vormt het een gesloten laag om het object heen. De coatingdikte kan variëren, afhankelijk van de toepassing en de wens van de opdrachtgever. Bij Kalfsvel kunnen we coatings van heel dun tot dik en ruwe structuur aanbrengen door te variëren in de micron per poedercoating (µm) en de oventemperatuur.
Grote capaciteit in poedercoating, bij Kalfsvel in Zaandam
Op ons terrein bevinden zich meerdere poederinstallaties bestaande uit cabines voor het spuiten en ovens voor het uitharden, moffelen genoemd. De maximale capaciteit daarvan is 5.000 kg in een oven van 9,0 x 3,8 x 3,6 (lxbxh). Daarnaast hebben we nog een 2e oven met de afmetingen 7,0 x 3,0 x 3,0. Wilt u weten of ook uw onderdelen in onze poederinstallaties gecoat kunnen worden? Vraag het ons en we bespreken graag de mogelijkheden.
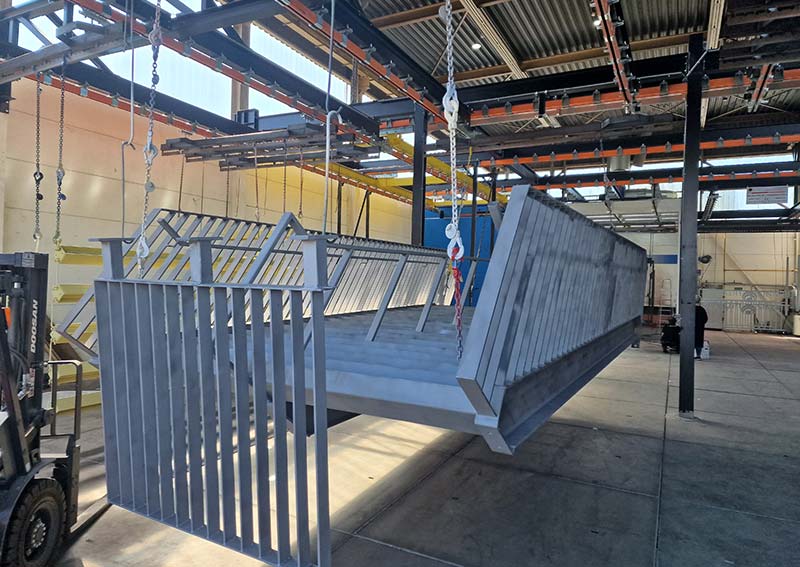